Tool holders: the perfect component with the right decision
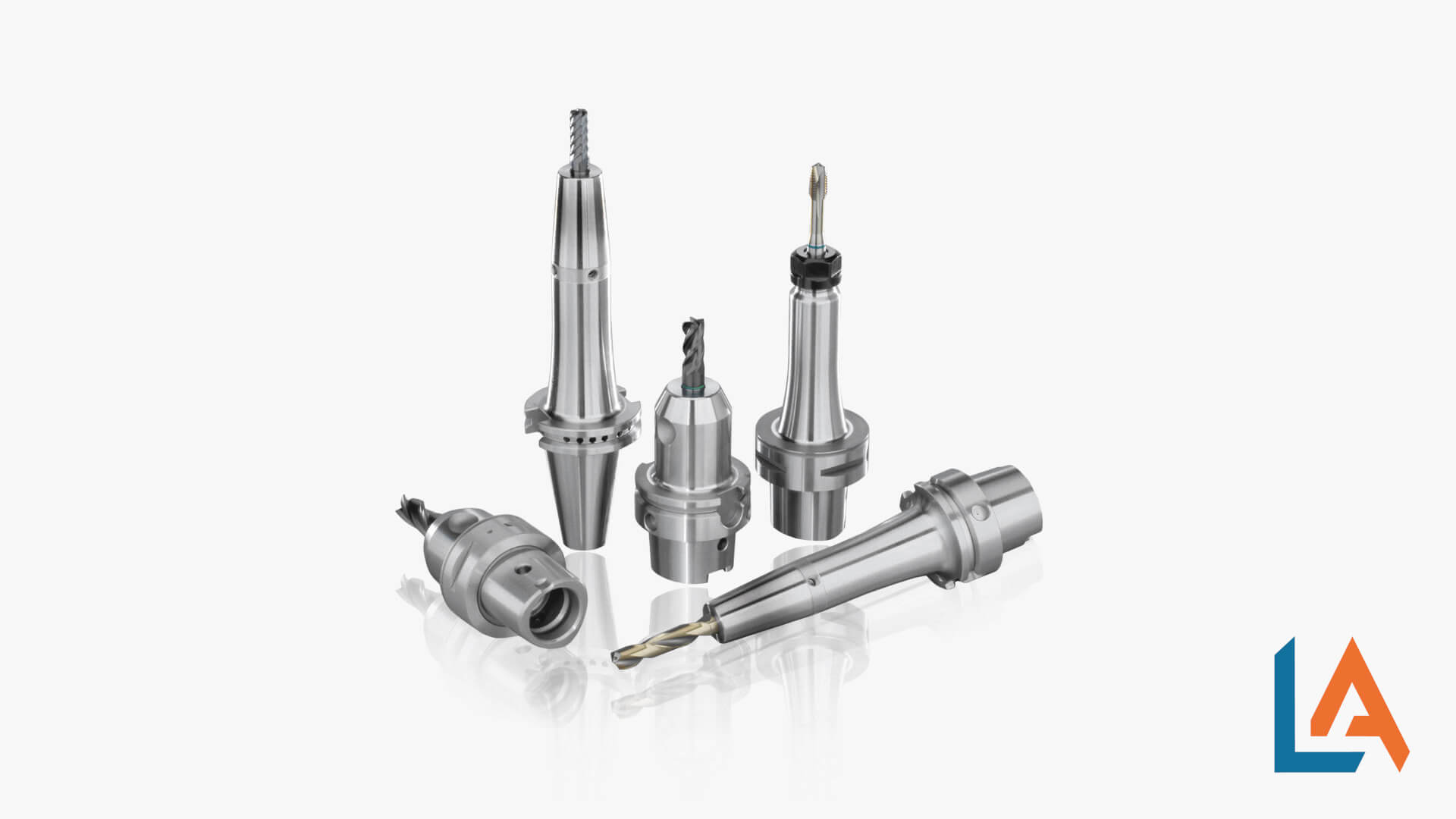
Clamping is an elementary function in the handling process. It is influenced by tool, workpiece, editing process and environmental, which are also interrelated with each other. Choosing a tool holder depends on the required component quality, accessibility and processing and is determined by variables such as processing speed, concentricity accuracy, clamping forces or clamping moments, to name just a few. It is often based on the user's many years of experience.
Tool holders: pros and cons
Collet chuck
+ cost-effective variant with frequently changing shaft diameters
+ requires little space
+ maximum flexibility
+ high stability
+ wide selection options
- Interfering contours due to the size of the collet chuck
- Clamping process prone to errors
Weldon food
+ simplest chuck
+ lowest purchase price
+ maximum holding forces
+ maximum ease of use
+ very widespread
- worst rounding cf. with other chucks
- inaccurate chuck
Shrink lining
+ high clamping force
+ maximum stiffness
+ concentricity accuracy < 3 μm
+ optimal accessibility
+ very good radial flexibility behavior
+ excellent holding power
+ suitable for high speeds
- Shrinking device required (additional cost)
- susceptible to vibrations
- Training for shredding equipment required. Not intuitive
- Space-intensive. A separate holder is required for each shaft diameter
Hydraulic tensioner chuck
+ high clamping force
+ high stiffness
+ concentricity accuracy < 3 μm
+ good accessibility
+ long service life
+ high vibration damping
+ suitable for high speeds
+ no additional tools required
- sensitive to contamination
- limited at high temperatures