Maximum efficiency in machining - tips for the right cutting data
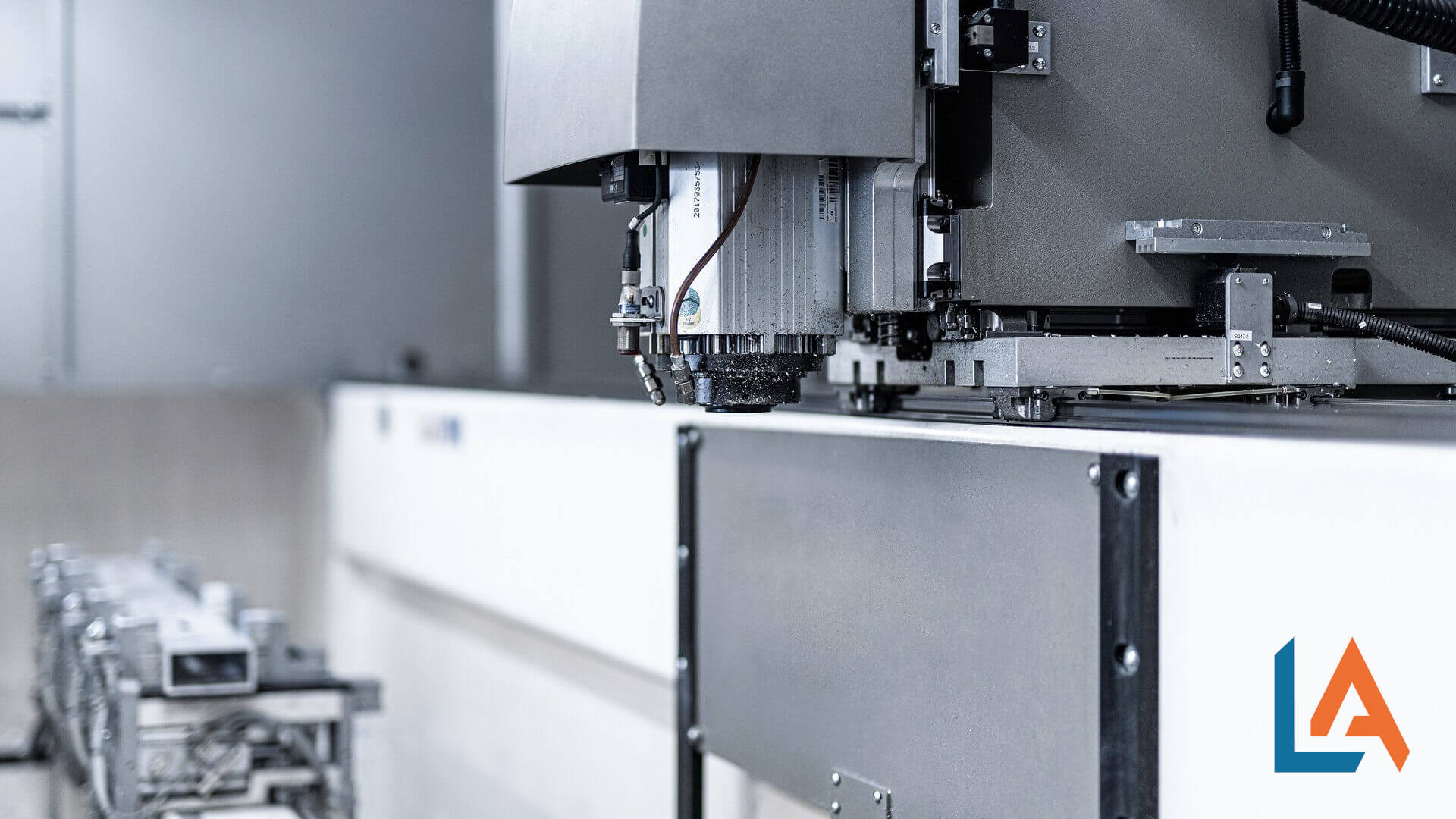
In our latest article, we are pleased to present you with some key information on cutting data for cutting tools. Choosing the right cutting data is crucial to achieve maximum efficiency, precision and tool life in machining. Read on for some key tips and recommendations that will help you get the best results from your machining processes.
1. Knowledge of materials is crucial
Before you define cutting data, it is essential to know exactly the material to be processed. Different materials require different cutting speeds, Advances and tool geometries. Make sure that you have all the necessary information about the workpiece material to be able to select the correct cutting data.
2. The importance of cutting speed
The cutting speed is one of the most important variables when defining cutting data. It not only influences the surface quality, but also the Tool life. Be sure to use the optimal cutting speed for the selected tool material. A value that is too low may result in excessive wear, while a value that is too high may impair the surface quality.
3. The right feed
The feed rate per tooth is another critical factor when determining cutting data. It influences the chip formation And the Tool life significantly. It is advisable to adjust the feed so that optimal chip formation and minimal wear are achieved. If necessary, experiment to find the best value.
4. Tool selection and geometry
Choosing the right tool and its geometry is crucial. Take into account the tool type, which cutting edge length and the tool radius. Tool selection should be based on the specific requirements of your cutting application.
5. Cooling and lubrication
Don't forget the importance of cooling and lubrication. Adequate cooling can the Tool life extend and the Quality of processed surfaces improve. Use the correct coolant and ensure that it is properly supplied.
6. Monitoring and adjustment
Cutting data should not be regarded as fixed quantities. Monitor your machining processes carefully and adjust cutting data as needed. The regular review and optimization of cutting data leads to continuous improvements in terms of efficiency and quality.
7. From practice
In this example, we will work on aluminum profiles with our cutter.
Aluminium has a cutting speed (Vc) of
- 100 - 200 m/min for hard aluminum alloys
- 100 - 500 m/min for soft, long-cutting aluminum alloys
tool
- VHM end mill ø 10 x 20/60/100 mm, Z1
At a processing center of Schirmer or BJM/BDM This cutter can be operated as follows:
- Speed: 18,000 rpm
- Milling feed: 2160 - 2340 mm/min
- drilling rate 600 mm/min
These machines have a small processing window. This ensures low-vibration tension of the profile and thus enables this cutting data.
The situation is different again with SBZ 122 of Elumatec.
This processing center has two serious drawbacks.
1. In most cases, only three clamps are used to clamp the profile.
This creates an unnecessarily large processing window.
2. The Z axis does not run simultaneously with the X and Y axes.
As a result, the processing from the front or back is smaller than from above.
This results in the following cutting data:
- Speed: 14,000 rpm
- Milling feed: 1260 - 1540 mm/min
- drilling rate 450 mm/min
The oil must be permanently sprayed onto the tool during processing.
In the world of machining Is the right choice of cutting data the key to successful processing processes. Use the tips above to optimize your machining operations and achieve top-notch results.