What is drag finish: Perfect surfaces for demanding products
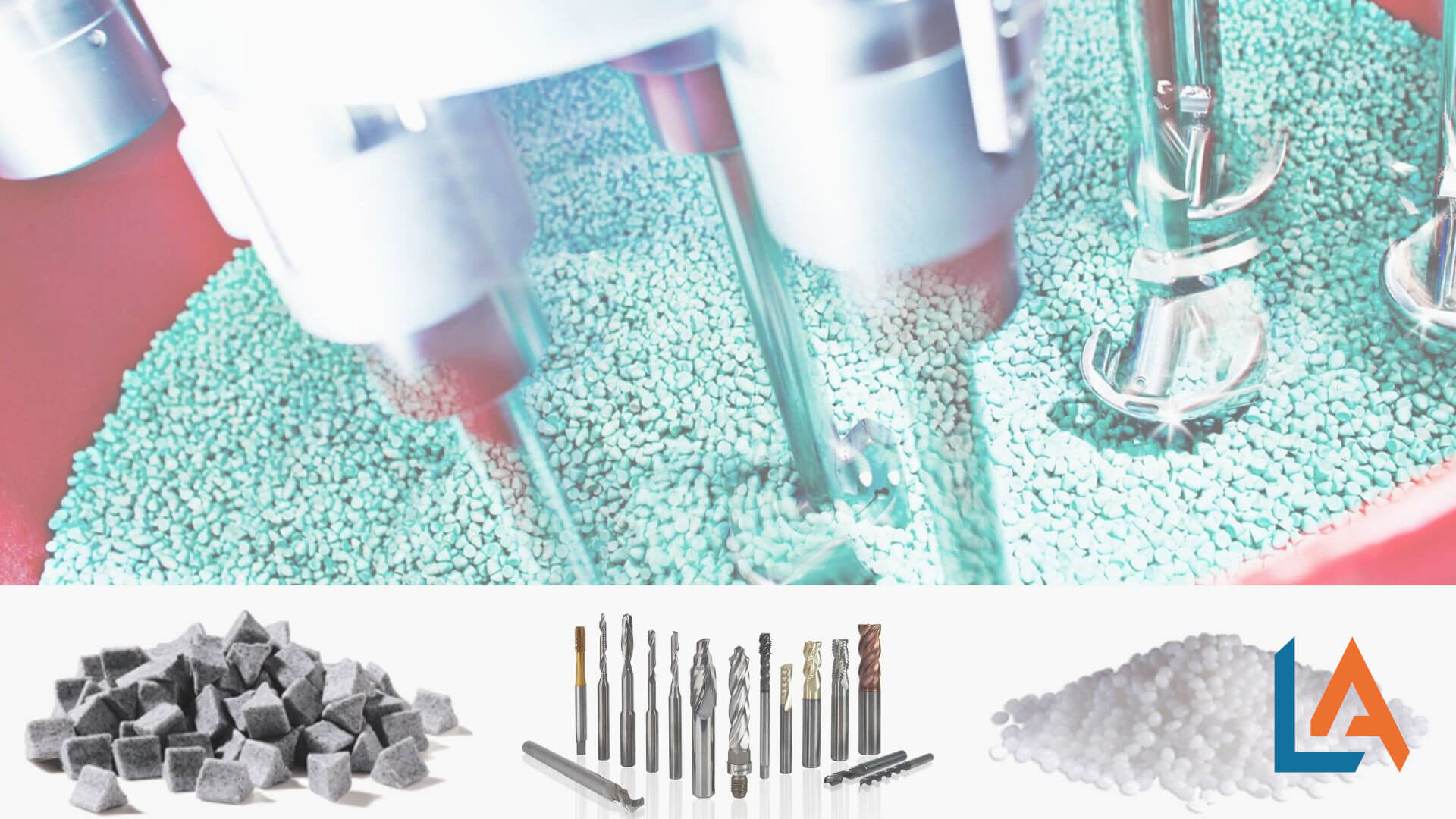
What is drag finish and what is it for?
What is drag finish?
Drag finish is a mechanical processing process that uses workpieces with the help of Towing bodies be processed in a rotating drum or container. These towing bodies, which often come from plastic or pottery exist, are with abrasive grains or polishing agent coated. The movement of the drag bodies results in controlled removal or smoothing of the workpiece surface.
Applications of drag finish:
The drag finish is used in numerous industries. It is often used to precision components, cutting tools, jewelry, medical implants, electronic components and optical parts to edit. The process makes it possible to remove burr, smooth surface roughness, produce mirror-smooth surfaces and round off edges. In addition, the drag finish can also be used to remove oxidation layers or to clean workpieces.
Advantages of drag finish:
Precise surface treatment: Schleppfinish enables targeted control of surface structure and roughness to meet specific requirements.
Material efficiency: Compared to other processes such as grinding or polishing, drag finishing removes less material, which saves material costs.
Consistency and reproducibility: The process ensures consistent surface quality, even with large quantities.
Automation potential: Schleppfinish can be automated, leading to more efficient production processes.
Key aspects of drag finish:
Selection of towing bodies: The choice of the right towing body depends on the type of workpiece and the desired processing result. Different shapes, sizes and coatings of the towing bodies influence the result.
Process parameters: Rotation speed, filling quantity, grain size, processing time and additives are decisive parameters that influence surface treatment.
After-treatment: Depending on requirements, it may be necessary to clean, rinse or dry workpieces after the drag finishing process.