Understanding the angles on a cutting wedge: The key to effective cutting technology
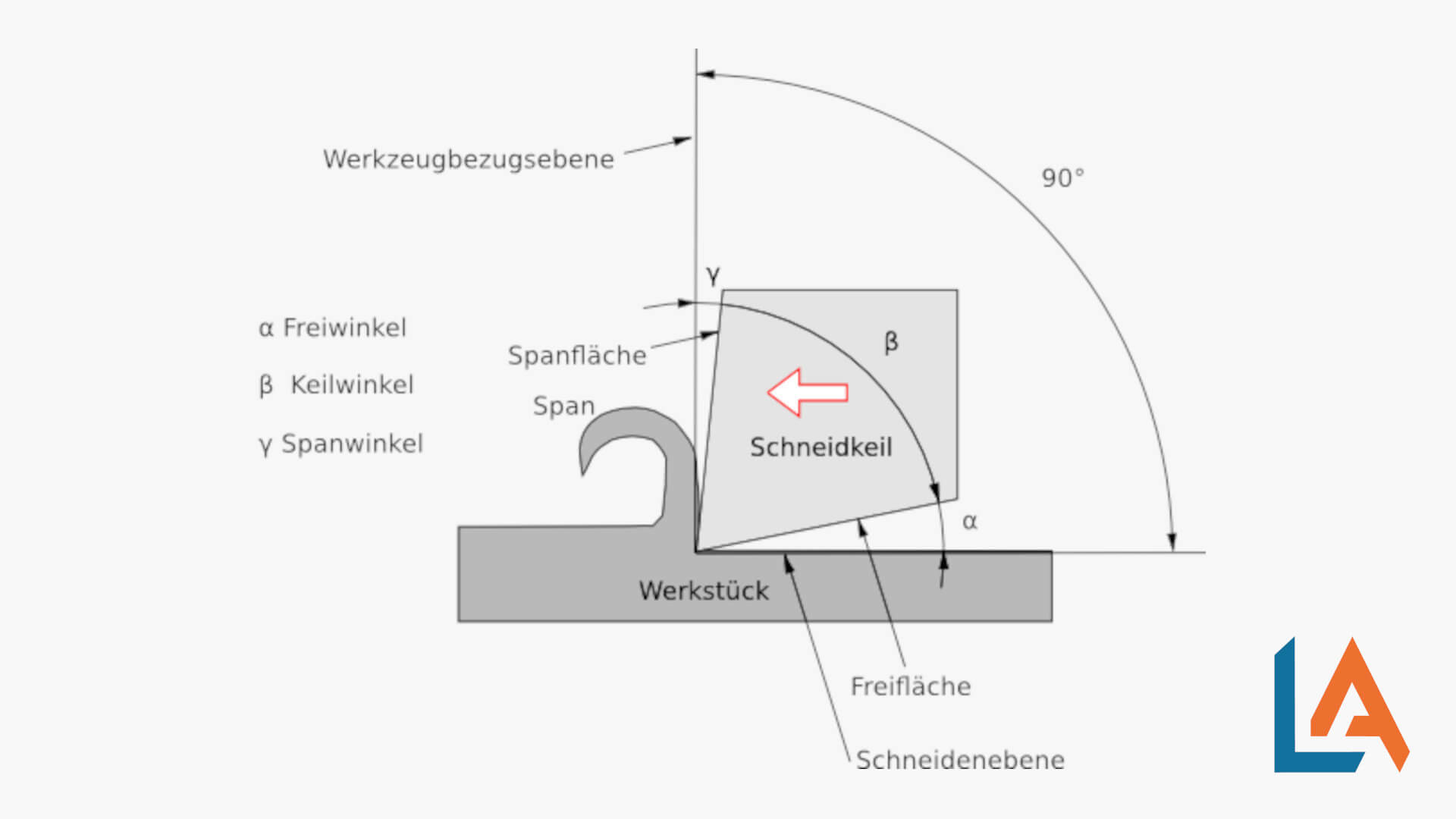
The basic shape of the blade for all cutting tools is the wedge. The inclination of the wedge-shaped tool blade significantly determines the cutting effect.
Wedge angle β
This forms the tool wedge and is located between the cutting surface and the open surface. Small wedge angles are sufficient to process soft materials. The smaller the wedge angle, the easier it is for the cutting edge to penetrate the surface of the workpiece and the lower the force required. The harder the material to be processed and the greater the chip thickness, the larger the wedge angle must be.
Free angle α
When the chip is removed, the free surface of the tool is “free” on the surface of the workpiece, does not press and does not cause excessive friction or heating.
Excessive friction on the open surface results in excessive tool wear, high power consumption and a rough workpiece surface. As a result of too much heating, the tool also loses its hardness and the blades quickly become dull.
Span angle γ
This angle is between the cutting surface of the cutting edge and a normal on the processing surface.
The rake angle has the greatest influence on chip formation and chip outflow.
The softer the material to be processed, the larger the rake angle is selected.
The larger a positive rake angle is, the less strongly the separated chips are bent, the easier they flow off and the lower the force required.
When working with high cutting speeds, interrupted cutting or very hard and brittle materials, small or negative rake angles are used.
If the rake angle is to the right of the normal, this is called a positive rake angle.
The angles of a tool blade are selected so that the cutting edge lasts as long as possible. The selection is therefore based on the following criteria:
· Hardness and toughness of the cutting material
· Hardness of the material to be processed
· Removal of heat generated by friction
· Guidance of the tool on machines