Aluminum processing made easy
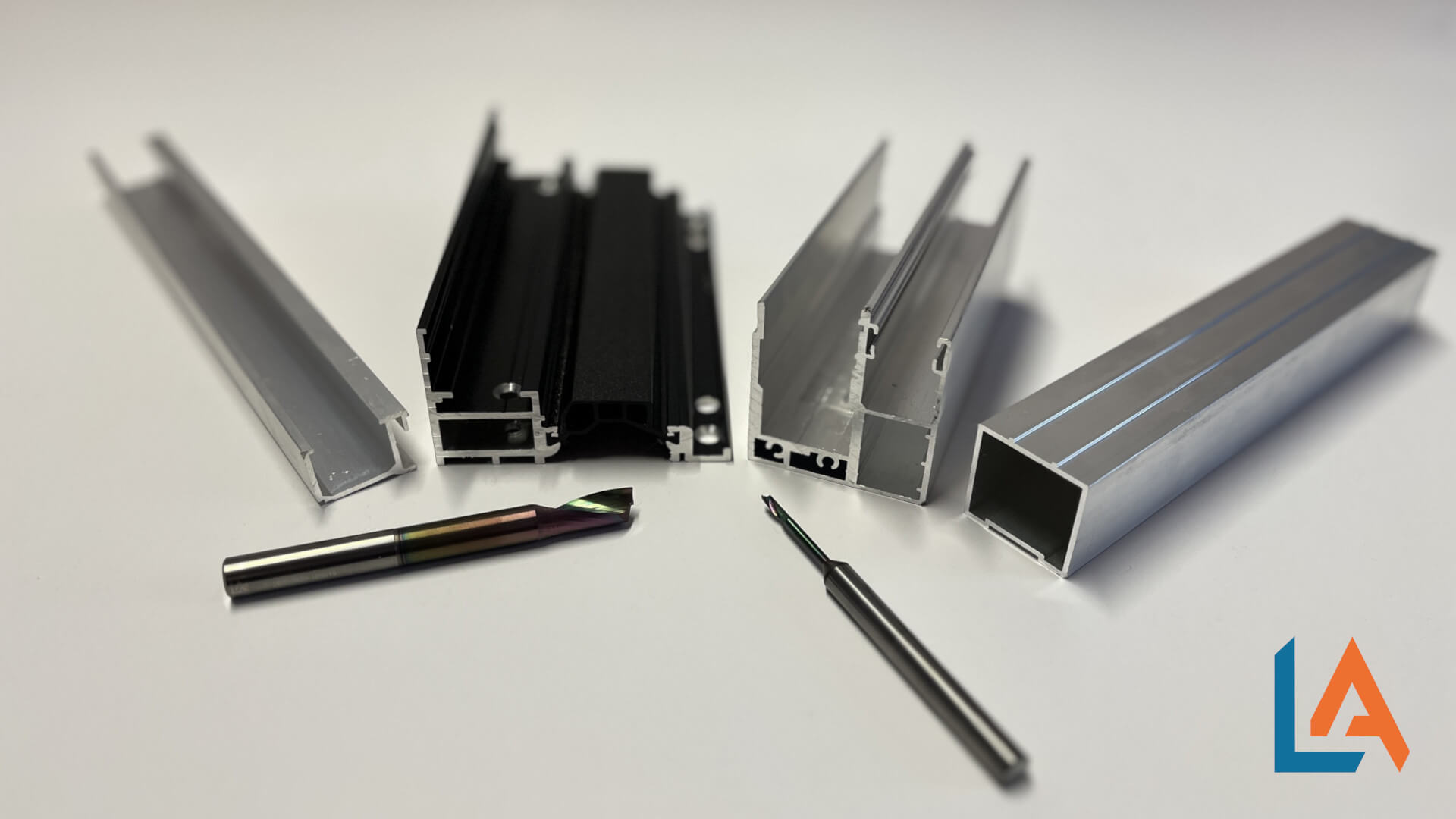
Aluminum is widely used in Aerospace, where it is used to build aircraft and spacecraft due to its low weight and high strength. In the automotive Aluminum is increasingly being used to manufacture vehicle bodies and components, which helps to reduce overall weight and improve fuel efficiency.
Also in electric vehicles Aluminum plays a key role.
In construction industry Is aluminum used for window frame, doors, facades and supporting structures used as it is corrosion-resistant and durable.
Die packaging industry relies on aluminum in the form of cans, slides and food packaging.
In the electrical engineering Is aluminum used because of its electrical conductivity used in transmission lines and cables. At the same time, it is in the electronics per heatsink and device protection housing popular.
Die shipbuilding industry uses aluminum for Ship structuresto reduce weight and increase corrosion resistance.
In the area of Traffic and transportation Do aluminum profiles come in trains, truck and bicycle frame used to increase efficiency.
Even in the Sports and leisure industry will sports equipment like golf clubs, bikes and camping equipment made of aluminum.
In addition, aluminum is used in medical devices, solar energy plants, wind turbines And even Indians military technology per Vehicle armor and protective equipment used.
In addition to the ease of processing, there are a number of other factors that speak in favor of the frequent use of aluminum:
- corrosion resistance
- High conductivity (electrical & thermal)
- When in contact with oxygen, it forms a protective oxide layer
- Light and sturdy metal
When processing aluminum, there are several important points that should be considered to achieve optimal results and avoid problems.
Here are the key points:
Tool selection
Tool material: Hard metal or diamond tools are good because aluminum is relatively soft. But the material can also lubricate when cutting.
cutting angle: A large clearance angle (10°-15°) is recommended to prevent the formation of buildup edges.
Cutting geometry: Sharp blades reduce friction and prevent the material from attaching to the tool edge.
Lubrication and cooling
coolant: Aluminum tends to heat up when cut, which can cause melting and sticking. Therefore, a suitable coolant should be used.
Minimal quantity or wet lubrication: These techniques help to optimize lubrication and cooling.
RECOMMENDATION: Our oil-free coolant Green CNC
cutting speeds
High cutting speed: Compared to steel, aluminum allows higher cutting speeds. VC 400 — 500 m/min
Adjust cutting speed: Speeds that are too high can result in tool wear and abrasion.
Processing process
Milling, turning, drilling: Different processing methods require different cutting parameters. Aluminum is easy to machine, but special tools for soft materials are recommended.
Machinability: Aluminum is generally easy to machine, but the properties vary depending on the alloy.
surface treatment
Polishing and sanding: Aluminum is sensitive to surface treatments, so fine grains and special abrasives are required.
Anodize: After processing, anodic oxidation can be applied to increase corrosion resistance.
Thermal expansion
Expansion coefficient: Aluminum has a high coefficient of thermal expansion. During processing, this must be taken into account when tolerances are tight.
Vibrations and chatter marks
Aluminum tends to generate vibrations and chatter marks during processing, which can be minimized by using stiff machines and clamping devices as well as optimized cutting parameters.
Bonding and welding
In downstream processes such as bonding or welding, the chemical surface properties of the aluminum after processing should be taken into account.
Each of these points is important to ensure high precision and quality when processing aluminum.